How to Choose a Medical Plastic Injection Molding Manufacturer
- Elite Precision Plastics
- Mar 28, 2024
- 5 min read
Updated: May 3, 2024
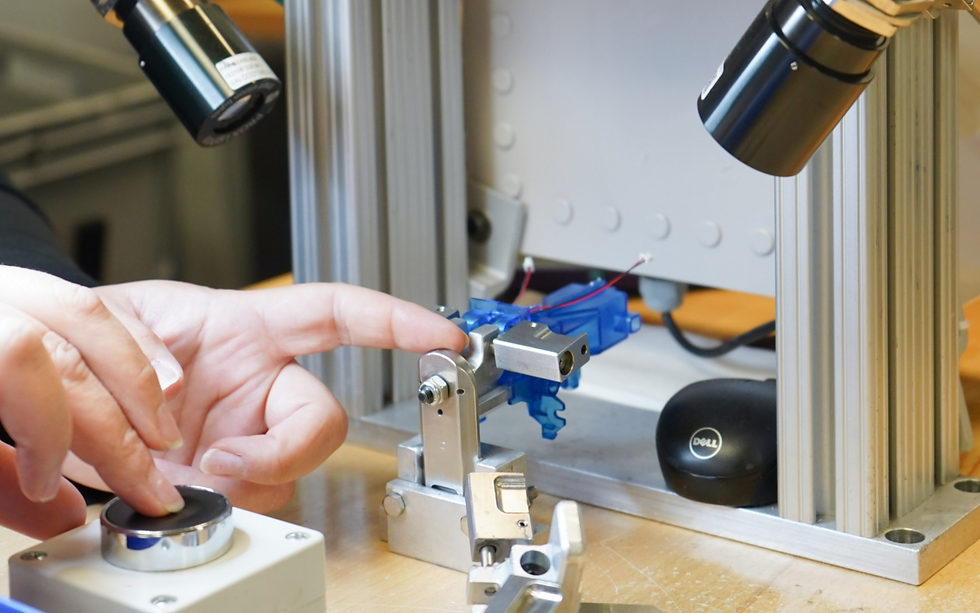
Plastic injection molding is one of the most agile methods of precision plastic production, making it an ideal way to manufacture leading-edge medical products. And the healthcare industry is taking notice, with a growing number of medical plastic injection molding manufacturers entering the industry and the global market expected to reach $37.8 billion by 2033.
Amid this growing number of manufacturers, choosing a partner to handle the complexities of medical plastics manufacturing requires careful evaluation. Your choice of a contract manufacturer will impact product functionality, reliability, and safety. The decision also affects costs, efficiency, time to market, and overall risk.
Below, we discuss some of the most important factors to consider when selecting a medical plastic injection molding partner, including key characteristics and questions to ask during the evaluation period.
Qualities of a Stand-Out Medical Plastic Manufacturer
Two areas clearly reflect the caliber and reliability of a contract injection molding manufacturer: its business model and experience in the field.
Values-driven business model
Every business must consider its bottom line, but when a manufacturer prioritizes profit above all else, they’re more likely to make choices based primarily on cost savings. This can result in lower-quality products, which may compromise safety. In contrast, a manufacturer that establishes its business model on a foundation of core values, trust, and reputation will more likely consider quality, dependability, and what’s best for their partners and end users when making decisions.
Ultimately, this can create more favorable profit margins for manufacturers and their partners over the long term, compared to profit-driven businesses that rely heavily on short-term cost-cutting methods.
Medical manufacturing experience
Manufacturing expertise comes from years of injection molding production. In the healthcare field, it’s important to also consider the manufacturer’s experience in delivering quality medical components. This indicates that the partner understands the complex requirements of high-precision injection molding in healthcare and biomedical applications and recognizes that tight tolerances are critical for patient safety.
A seasoned manufacturer is also more likely to have invested in a highly trained team and cutting-edge equipment to ensure that every product fits precisely within specifications, with capabilities that may even exceed the tolerances set by regulatory standards.
“When you talk about tolerances that are within five thousandths of an inch, you have to have the right equipment to meet that tolerance,” says Nate Schlauch, Director of Manufacturing at Elite Precision Plastics. “If you don't have a machine that has those capabilities, let's say it's an old hydraulic machine, it will be difficult to meet that tolerance consistently.”
What to Look for in a Medical Plastic Injection Molding Partner
When evaluating a manufacturer, look for a partner whose values align with the mission of advancing healthcare. A business that’s committed to safety, quality, and transparency will demonstrate those values across its culture, customer relationships, and reputation.
The following questions can reveal essential details about a potential partner’s business approach, production practices, and commitment to quality control.
What engineering and design support do they offer?
A plastics manufacturer that offers comprehensive engineering and design support will enhance production at every stage. For products already on the market, the manufacturer may be able to offer an existing mold in-house. For products still in the concept phase, the manufacturer’s engineering team should be able to work with the customer across the entire process, from R&D through material selection, prototyping, testing, and market production. This kind of close collaboration can help identify potential issues early on, enhance manufacturability, and ensure the final product functions optimally while complying with regulatory standards.
Do they have any certifications?
Certifications benchmark a manufacturer’s commitment to quality and compliance. The International Organization for Standardization (ISO) offers certification programs for companies that meet its high standards for quality control. The most important certification for medical manufacturers is ISO 13485:2016. This standard was developed to ensure that medical device components function optimally to keep patients safe. Another standard, ISO 9001, focuses on quality management systems (QMS), which facilitate rigorous quality control.
What other quality control processes are in place?
While certifications are a helpful evaluation tool, they don’t guarantee that a business consistently follows all regulatory requirements. A high-quality injection molding manufacturer should be able to produce documentation of its QMS, internal audits, external audits by the FDA or certifying bodies, in-process inspections, and quality assurance protocols.
Beyond requesting documentation, ask potential partners for a full demonstration of their QMS, ideally in person. Let them know you intend to conduct your own regular audits should the contract move forward.
How easily can you communicate with members of their team?
Medical plastic injection molding is a complex process; you may need to connect with the manufacturer at any moment or vice versa. The communication channels that a contract manufacturer makes available will define your ability to make last-minute adjustments, request products on short notice, and shape your overall relationship.
Communication is key in a partnership. If you have an issue with your parts, you want a quick response and a partner that is willing to resolve these issues quickly and stand with you in those difficult times. As what issue resolution processes your prospective partner has, such as the Six Sigma DMAIC methodology.
Working with a U.S.-based manufacturing partner can streamline communication, as well as facilitate meeting the team in person, touring the facility, and viewing a QMS demonstration.
Do they have cleanroom facilities?
Many medical products require contamination-free production. Cleanrooms are controlled environments that eliminate dust, micro-particles, and other contaminants. Ask potential partners about air filtration, temperature and humidity controls, and employee protocols if you require cleanroom manufacturing.
Do they offer secondary services?
Using different contractors for secondary services, such as assembly, pad printing, or laser etching, can increase costs and complicate production logistics. A manufacturing partner with in-house secondary capabilities can streamline the production process, reducing time-to-market and adding logistical and financial benefits.
Additional considerations
A manufacturing contract comes with complicated concerns that your legal team must address. But you can bring up some important considerations when vetting a contract manufacturer, such as:
Materials: Will the manufacturer use virgin material or regrind material?
Dedicated process: Will your mold have a dedicated press and process?
Quality assurance: What are the manufacturer’s installation qualification (IQ), operational qualification (OQ), and performance qualification (PQ) processes for your mold?
Intellectual property: Does the manufacturer have a reputation for honoring NDA agreements?
Warranties: Will they provide warranties for both parts and molds?
Liability: Will the manufacturer assume some of the risk of product failure, or will you be on your own in the event of a patient event or recall?
Ensure that you’re entering into a successful partnership by doing your due diligence when vetting a medical plastic injection molding manufacturer. Knowing what to look for in manufacturing partner can be the key to getting a reliable and safe finished product efficiently, and cost-effectively.
Elite Precision Plastics is an experienced ISO 13485-certified injection molding manufacturer specializing in high-quality, tight-tolerance manufacturing. Contact us to learn more about our U.S.-based manufacturing services.